Drill String Design Calculations Steps
This article covers simple drill string design steps for vertical and directional wells.
Drill Collars Size & Weight Selection
Unless mechanical hole sticking is a problem, the largest diameter drill collars consistent with other needs are generally best. Their increased stiffness means more directional and drill bit stability. Also, they will have fewer connections for a desired weight on bit and therefore a shorter BHA which can lessen the probability of differential sticking.
Larger OD collars in a given hole also means less lateral freedom of movement in the BHA. This decreases buckling stress and the rate of connection fatigue. In practice however, drill collar size is often determined by existing rig inventory. Other factors which come into play are:
Fishability considerations
Capabilities of the rig handling equipment
Directional control requirements
Hydraulics
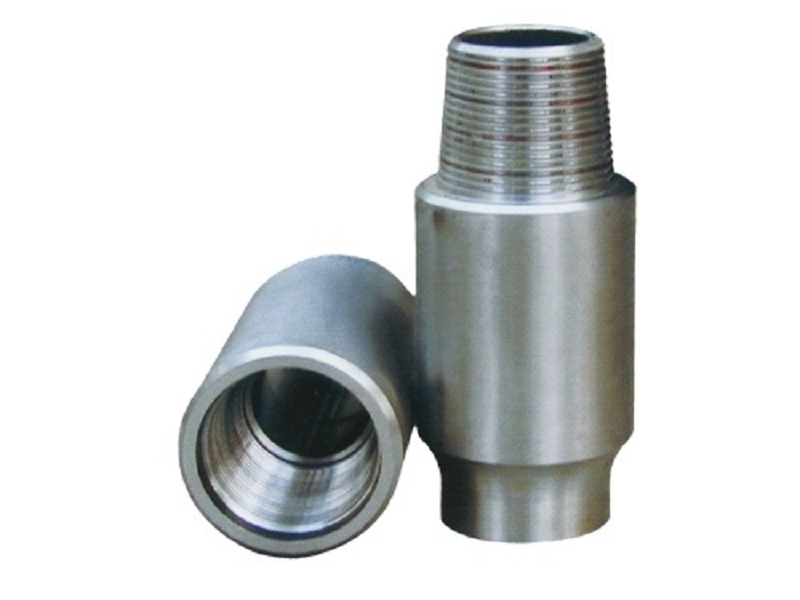
Desired exterior features (spiral grooves, elevator grooves, or other features).
One of the drill string functions is to produce the sufficient weight to drill the hole so how many drill collars you will need to deliver the desired WOB. Mainly there are two methods used in drill string design for the Drill collar weight Calculation.
Drill Pipes Selection
The first thing to consider while running the drill string design calculation is to check if the drill pipes you are going to use will be able to sustain the drill collars and BHA loads in the worst cases which is the stuck. So the first thing is to check your drill pipes.
Maximum Over Pull
Drill string design needs from you to check the maximum over pull you can apply to drill string without drill pipes failure. It is easy to be done just remember don’t exceed 80% of drill pipes yield strength.
Slip Crushing
Slips exert hoop compression on the drill pipe which can deform the pipe if conditions are unfavorable. It will be important in drill string design to check if slip crushing may happen to your drill pipes or not.
Drill Pipes Collapse Pressure
If the drill pipe is subjected to an axial tensile load, the collapse pressure ratings which will be used in drill string design, from the tables must be derated. So you will have to calculate the effective drill pipes collapse pressure.
Drill Pipes Burst Pressure.
The differential pressure acting across the drill pipe wall due to an internal pressure greater than the external pressure is known as the burst load. You will have to check the used drill pipes burst pressure.
Tool joint torsional strength
Assume that the produced torque during drilling proceed make up torque of drill pipes tool joints or the torsional strength of drill pipes, then what will happen. So check the tool joints torsional strength. And drill pipes torsional strength is important during the drill string design calculations.
Heavy Weight Drill pipes
The field tests showed that the higher the stiffness ratio at the transition zone, the greater the fatigue build up. In Heavy Weight Drill Pipe Specs & Selection, we shall cover the following subjects:
Heavy Weight Drill Pipes Definition
Heavy Weight Drill Pipe Function
Heavy Weight Drill Pipe Specs
Heavy Weight Drill Pipe Specs Sheets From work strings international
Heavy Weight Drill Pipe Specs Selection and Design
Use of HWDP offers the following advantages
Select BHA Connections and Features
The following points apply not only to drill collars and Heavy Weight Drill Pipe from the rig inventory, but also to the many specialized tools that find their way into the hole. Stabilizers, Mud Motors, Measurement While Drilling and LWD tools, hole openers, under-reamers, Drilling jars and many other tools are all subject to fatigue
Bending Strength Ratio
In Bending Strength Ratio article, you shall discover its definition, ranges and you can download its calculator.
BHA Connection Thread Form
Thread forms with full root radii should be used in all BHA connections to maximize fatigue resistance. API Regular, NC and 5.1/2 Full Hole connections meet this requirement, though the API NC thread form (V-038R) is superior to the others. The H90 thread form is also considered acceptable even though it does not have a full root radius.
Stress Relief Features:
Stress relief features as described in API Spec 7, should be specified on all BHA connections NC-38 and larger. These features include the “stress relief pin” and “boreback box”. They extend connection fatigue life by eliminating on-engaged thread roots which act as stress concentrators.
Stress relief features are beneficial on HWDP connections. Pin stress relief grooves are not recommended for connections smaller than NC-38 because they may weaken the connection’s tensile and torsional strength and because fatigue is often less of a problem than static loads on small connections. Boreback boxes could be used on smaller connections without weakening them and should be considered if box fatigue is occurring.
Cold Rolling:
Cold rolling BHA thread roots and stress relief surfaces increases fatigue life by placing a residual compressive stress in the thread roots. Cold rolling is also beneficial on HWDP threads, though not on normal weight drill pipe tool joints. Fatigue is rarely a problem on normal weight drill pipe tool joints owing to the relative stiffness of the tool joint compared to the tube.
BHA Connection Torsional Strength:
Since torsion is transmitted from the top down, BHA connections are usually subjected to lower torsional loads than the connections above. However, if “stick/slip” is occurring, or if you are running a tapered or “slim” assembly, especially one using PAC connections, torsional strength should be checked to confirm that it is greater than the expected operating torsion at the BHA.
Tool joint torsional strength tables cannot be used directly for this purpose because tool joint and drill collar materials have different yield strengths. However, drill collar connection torsional strength can be calculated by the following formula:
TS=MUA/F
And
TS |
= |
DC connection torsional strength (ft-lb) |
MUT |
= |
DC makeup torque (ft-lb) (O.C.T.G. Procter Drill String Design Manual) |
F |
= |
The factor “f” is simply the decimal fraction of torsion yield strength that forms the basis for the makeup torque value . ( It is different according to Pipe Manufacturer) |