The corrosion of drill pipe Introduction
Drill pipe is one of the main tools used in oil and gas exploration and development, accounting for 80% – 90% of the total length of drill string. In the process of drilling, the failure of drill pipe is a very serious problem.
Although the torque, tensile strength, compressive strength, bending stress, etc. of the drill pipe are accurately calculated under ideal conditions before drilling, the corrosion of the drill pipe in the drilling fluid during the actual drilling process makes the drill pipe failure more than expected.
According to the statistics of the drilling tool failure analysis project undertaken by China Petroleum Pipe Research Institute in 2006, the total number of drill pipe failures reached 17 out of 32 drilling tool failure projects, accounting for 53.2% of the total number of drilling tool failures.
More than 60% of drill pipe failure accidents are related to its corrosion behavior in drilling fluid.
An American drilling company once made such statistics that more than 75% of all drill pipes degraded or scrapped by the company were caused by internal wall corrosion (comprehensive corrosion, pitting corrosion, corrosion fatigue, etc.).
It can be seen that corrosion is the main cause of drill pipe failure. And corrosion makes the inspection, maintenance and accident treatment of drill pipe reduce the drilling efficiency and increase the cost.
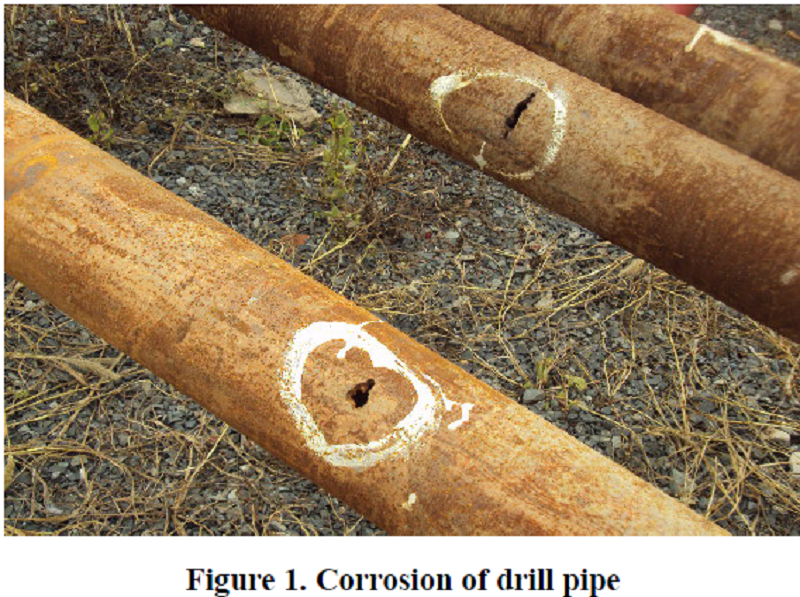
1.Drilling failure
The service conditions of drill pipe include: the load properties (static load, alternating load, impact load), loading sequence (load spectrum), stress state (tension, compression, bending, torsion, shear, contact and various composite stresses), temperature, chemical medium (drilling fluid, air and gas, water, H2S, CO2, dissolved salts) and pressure, etc.
The drill pipe may encounter corrosive environment in deep well drilling, with temperature exceeding 260 ℃ and gas pressure exceeding 2 × 108Pa, the concentration of CO2 and H2S exceeds 1%, and the aqueous phase containing Cl – and dissolved salts of organic acids.
The failure forms of drill pipe mainly include brittle fracture, fatigue, corrosion fatigue, corrosion damage, etc.
Most of them are corrosion fatigue failures. These failure forms often exist at the same time and interact with each other.
Therefore, when analyzing the failure of drilling tools, we should distinguish the main failure form from the secondary failure form according to the characteristics of various failure forms, as well as the differences and connections between various failure forms, so as to take active and effective measures to prevent or reduce the failure accidents of drill pipes.
2.1 Chemical medium causing corrosion
2.1.1 Drilling fluid
The corrosivity of various drilling fluids is: (aerated seawater drilling fluid, potassium based polymer drilling fluid, low pH polymer drilling fluid, H2S contaminated drilling fluid)>(low pH natural drilling fluid, salt water drilling fluid, fresh water drilling fluid)>(high pH natural drilling fluid, lime drilling fluid)>(highly dispersed drilling fluid, oil in water drilling fluid, saturated salt water drilling fluid)>(corrosion inhibitor treated drilling fluid, oil-based drilling fluid).
2.1.2 Oxygen corrosion mechanism
2.1.3 H2S corrosion mechanism
2.1.4 CO2 corrosion mechanism
3 Progress in anti-corrosion technology of drill pipe
Drilling corrosion control methods can at least be divided into the following three categories:
1) selecting appropriate corrosion inhibitors to reduce the corrosion of drilling fluid on drill pipes;
2) Select more corrosion resistant materials;
3) Apply proper surface treatment or plating treatment to drill pipe.
3.1 Chemical control
Chemical control mainly refers to the use of removers and inhibitors for dissolved gases.
3.2 Selection of corrosion resistant materials
In the process of drilling and production, there are many advanced technologies such as ultra-high strength steel (UHSS), aluminum drill pipe (ADP) and titanium drill pipe (TDP). These materials have higher corrosion resistance and fatigue resistance.
Aluminum drill pipes have been used for decades, and Russia has accumulated a lot of experience in using aluminum drill pipes in offshore drilling projects.
Aluminum drill pipe and traditional steel drill pipe have many advantages.
Lower quality, higher strength to mass ratio, better corrosion and fatigue resistance.
Aluminum drill pipe can be used in extended reach well drilling and horizontal drilling, but it also has many defects. Its yield strength is low, so it is seldom used in other projects.
3.3 Surface treatment and coating of drill pipe
1) Carburizing, carbonitriding, phosphating, and oxidation treatment can slow down the corrosion of drill pipes.
The surface hardening and tempering treatment can reduce the surface hardness and make the steel drill pipe better resistant to sulfide stress corrosion cracking and hydrogen embrittlement.
2) Conduct quenching and tempering treatment, salt bath carbonitriding, oxidation cooling, polishing and re oxidation treatment on SAE 4135 and SAE 4140 drill pipe steel. The corrosion fatigue tests were carried out at 5% NaCl with untreated substrate and materials with Ni-P coating on the surface.
The results show that the corrosion fatigue life of carbonitriding plus oxidation treated samples is higher than that of untreated and Ni-P coated samples.
The excellent effect of carbonitriding plus oxidation treatment comes from the good coverage of the oxide layer, which fills the hole with the oxide layer.
3) The use of thermal spraying tungsten titanide intermediate coating has slowed down the serious wear and corrosion of drill bits and downhole tools.
The tests and field tests of explosion spraying, laser spraying and vacuum furnace spraying show that explosion spraying has higher corrosion resistance than other methods.
4) The surface of Cr Mo alloy drill pipe material is plated with duralumin and subsequently treated.
Electroplated anodized duralumin has high hardness and wear resistance.
In recent years, sealing and dyeing treatment have been used to improve the corrosion resistance of electroplated duralumin, but the traditional sealing process has greatly reduced the wear resistance of the duralumin coating. Trivalent chromium ion sealing agents, including hydrothermal solution, nickel acetate, sodium dichromate, sodium silicate, nickel fluoride, black dye sealing agents, and black dye and nickel composite sealing agents, as well as their sealing process and properties, were studied in detail.